경주 경주 공장을 통해 바라본 텔스타 Smart Factory 이야기
페이지 정보
본문
2018년 2월 첫 양산을 시작으로 텔스타의 새로운 비즈니스 문을 연 주식회사 텔스타 경주 공장은, ‘3차원 레이저 커팅 시스템’을 활 용하여 핫스템핑 공법이 적용된 차체를 가공하는 공장이다. 나아가 이 곳은 우리가 지난 33년간의 경험을 통해 쌓아온 기술을 총동 원하여 국내 스마트팩토리 시범 공장이 되기 위한 목표를 가지고 설립되었다. 자동차 산업에서 다양한 조립기, 정밀 측정기 등의 맞 춤형 비표준 설비를 제작하고 운영하며 다져온 기본기를 바탕으로, ‘다양한 최신 스마트 기술들을 접목한 최적화된 공장 운영’이라는 목적을 달성하고자 했다. 목적이 분명한 시작으로 단기간에 ‘2019 중소벤처기업부 스마트팩토리 시범 공장’으로 선정된 경주 공장 은, 국내 스마트팩토리 모범 사례로 당당히 소개될 수 있는 공장을 만들어 내는 데 역량을 집중하고 있다.
Telstar Gyeongju plant, started mass production since February 2018, manufactures automobile body applied with Hot Stamping method by utilizing ‘3D laser cutting system’. The plant opened a door for Telstar’s new business. Furthermore, this factory was established with the goal of becoming a pilot plant for domestic smart factory by employing all of the technologies that Telstar has accumulated over the past 33 years. Based on the basic skills acquired by manufacturing and operating tailored non-standard equipment such as various assembly machines, precision measuring machines from automobile industry, the plant attempted to achieve a goal of optimized plant operation by applying many new smart technologies. Due to a clear goal from the beginning, it was selected in a short period of time as a pilot plant for smart factory in 2019 by the Ministry of SMEs and Startups. We are concentrating our capabilities on creating the plant that can be proudly introduced as best practices of domestic smart factory.
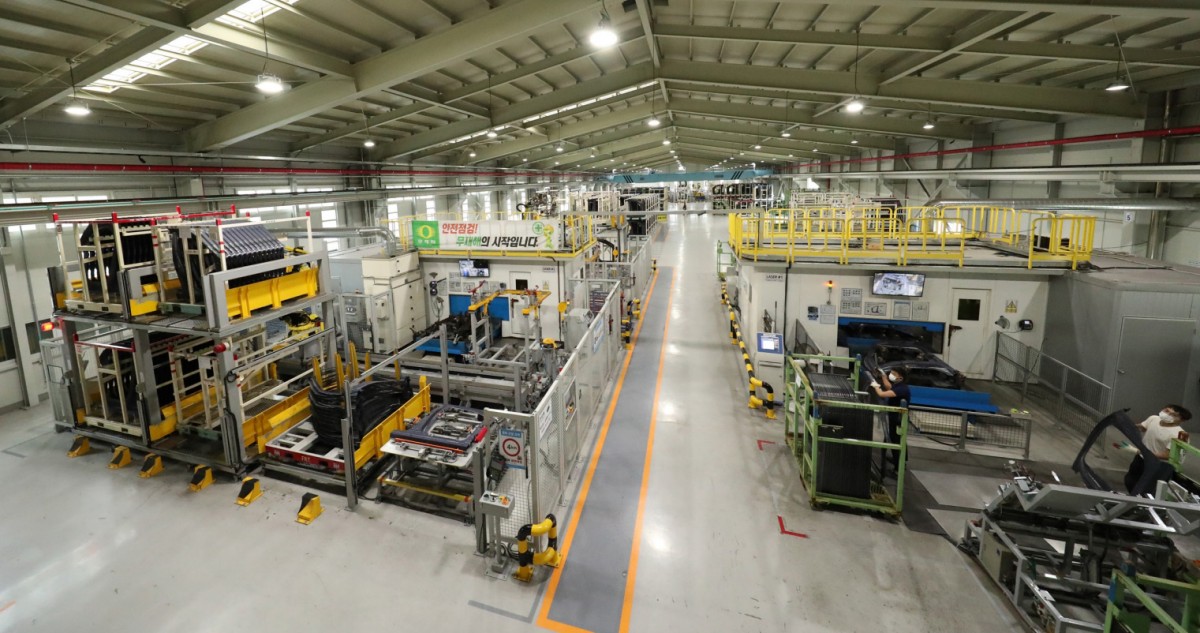
스마트팩토리의 첫걸음! Digital Transformation
스마트팩토리란 무엇일까? 이 물음에 전문가들은 다양한 정의를 내리 고 있지만, 텔스타는 가장 먼저 우리만의 스마트팩토리 핵심 개념을 정 립했다. “제조업의 영원한 숙제인 품질 확보(Quality), 생산원가 절감 (Cost), 재고가 없는 납기관리(Delivery), 끊임없이 변하는 시장의 환경 과 요구 사항에 민첩하게 대응(Responsiveness)할 수 있는 공장.” 이 것이 바로 텔스타가 말하는 스마트팩토리다. 우리가 흔히 스마트팩토 리를 상상할 때 쉽게는 자동화, 무인화된 공장 그리고 그 위에 각종 데 이터들이 복잡하게 연결되어 3차원 대시보드가 펼쳐지는 영화 속 장면 을 떠올린다. 이러한 상상 속 공장이 현실화되기 위해 가장 중요한 첫 걸음은 공장 내 모든 설비가 서로 상호 작용하며 스스로 제어될 수 있 게 하는 각종 데이터의 디지털화, 즉 Digital Transformation이 선행되 어야 한다. 결국 Big Data Management Technology에 의해 공장은 스 마트해지기 때문이다.
First step for smart factory! Digital Transformation
What is a smart factory? Experts define the answer to this question with various opinions, but before deciding which one is right or wrong, Telstar defined a key concept of smart factory by ourselves. “A plant that assures Quality, a perennial problem of manufacturing industry, decreases production Cost, manages Delivery without stocks, and has agile Responsiveness to ever-changing market environment and requirements.” This is the Smart Factory that the Telstar defines. When we simply imagine a smart factory, we can easily think of an automation, an unmanned factory, and a scene like a movie in which a 3D dashboard is unfolded where various data are intricately connected. In order to realize such an imaginary factory, the most important first step is digitalizing all data that enables all facilities in the factory to interact with each other and control themselves. In other words, Digital Transformation has to be preceded. In the end, the plant become smarter because of Big Data Management Technology
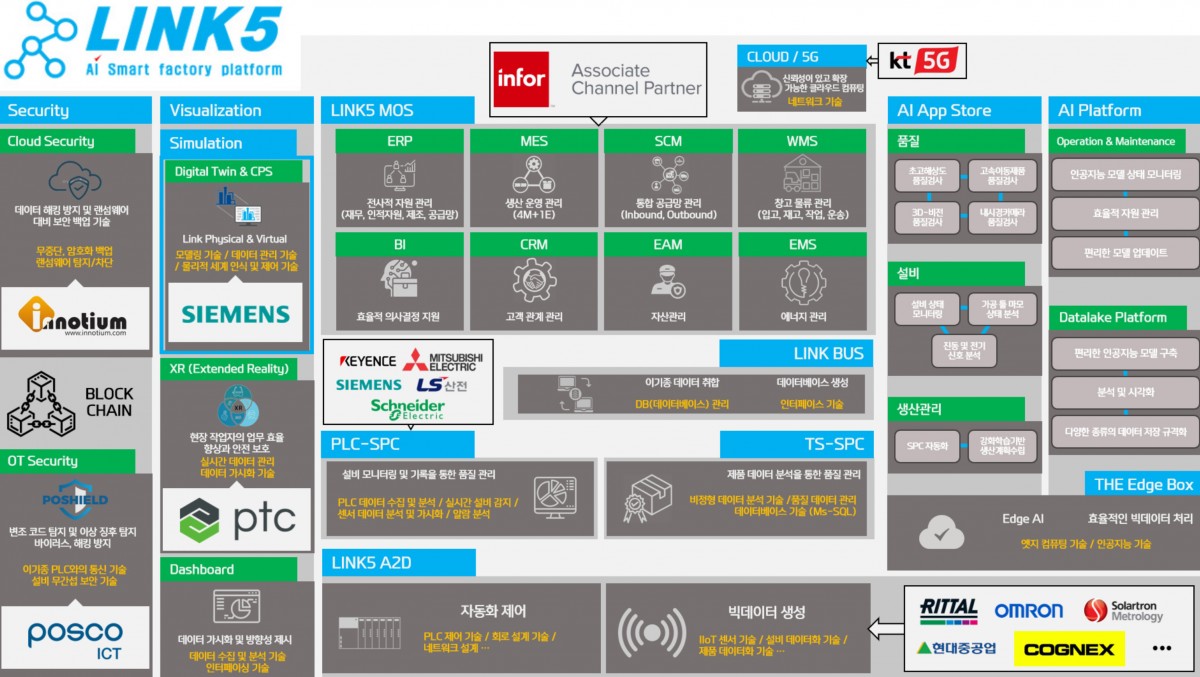
물류자동화를 통한 Data Creation
경주 공장 레이저 설비는 처음에 수작업 공정을 통해 생산 운영되었다, 이는 작업자의 경험과 숙련도에 영향을 받을 수밖에 없는 시스템이다. 단순하고 반복적인 작업 때문에 피로도가 높은 탓인지, 생산자의 잦은 변경 또한 생산 운영을 최적화 하는 데 걸림돌이었다. 우리는 이를 개 선하고 스마트화하기 위해 다양한 해법들을 검토하였고, 첫 번째 작업 으로 수작업 공정의 물류자동화를 진행하였다. 제품을 자동 공급하는 물류 설비 구축을 통해 기존 작업자는 단순 노동에서 설비를 운영하는 관리자가 되었고, 생산 제품은 동일하지만 품질과 생산성이 개선되는 효과를 볼 수 있었다. 무엇보다 중요한 것은 생산 과정에서 발생하던 다양한 정형, 비정형 행위들이 Digital Data로 생성되어 이후 과정에서 제어나 분석 활용이 가능하게 된 점이다.
Data Creation through logistics automation
The laser equipment at the Gyeongju plant was produced and operated through a manual process at first. Such system was inevitably affected by the experience and skill level of workers. Frequent changes by workers were also an obstacle to optimize production operations. They might be affected by high fatigue caused by simple and repetitive work. We have reviewed number of solutions to improve this issue and make it smart. As the first process, we carried out logistics automation of manual process. By establishing a logistics equipment that automatically supplies products, the operators, once worked for simple labor, became managers who operate equipment. In addition, the production products were the same, but the quality and productivity were improved. Most importantly, since various standard and non-standard actions occurred during the production process were generated as digital data, they could be controlled or analyzed and utilized in the subsequent processes.
데이터 분석 활용을 위한 생산 운영 시스템 LINK5 MOS
Digital Transformation을 통해 생성된 수많은 데이터들은 적절하게 분 석되고 활용되지 않는다면 의미가 없다. 무작정 많은 데이터를 모으는 것이 아니라, 꼭 필요한 데이터를 생성하여 목적에 맞게 활용하는 것이 중요하기 때문에 데이터 설계에는 전문가가 필요하다. 데이터를 활용 하는 방법에는 제조실행 시스템을 통한 직접 제어, AI 분석을 통한 예 지보전과 의사결정 시스템 구축 등 다양한 방법이 있다. 이러한 전산화 시스템이 구축되어 있지 않던 경주 공장은 ERP나 MES, SCM 등을 각 각 도입하는데 중소기업으로서 부담을 갖게 되었고, 우리는 이를 이해 해 각각의 시스템에서 기업에 꼭 필요한 일부 기능들을 통합한 생산 운 영시스템 MOS(Manufacturing Operation System)를 개발해 경주 공 장에 맞게 적용했다. 앞서 생성된 데이터를 DB에 모아 MOS에서 분석 및 변환하여 여러 시각 정보를 제공하게 되었고, 의사결정에 도움을 주 며 공장 운영에 효율을 높이게 되었다.
LINK5 MOS is a production operation system for utilization of data analysis
Even if lots of data generated through Digital Transformation is not properly analyzed and utilized, the generation become meaningless. It is important not to collect a lot of data recklessly, but to generate necessary data and use them for essential purposes. That's why experts are needed for data design. There are various methods to utilize data such as direct control through the manufacturing execution system, as well as predictive maintenance and decision-making system construction through AI analysis. In the Gyeongju plant where such a computerized system was not established, it was a burden as a small and medium-sized company to introduce various systems such as ERP, MES, and SCM. However, Telstar Hommel understood such situation and developed MOS (Manufacturing Operation System), a production operation system that integrates some of the essential functions to the company in each system, and applied it. Various visual information was provided by collecting previously generated data in a data base and analyzing and converting them in the MOS. As a result, the system helped decision making and improved efficiency in plant operation.
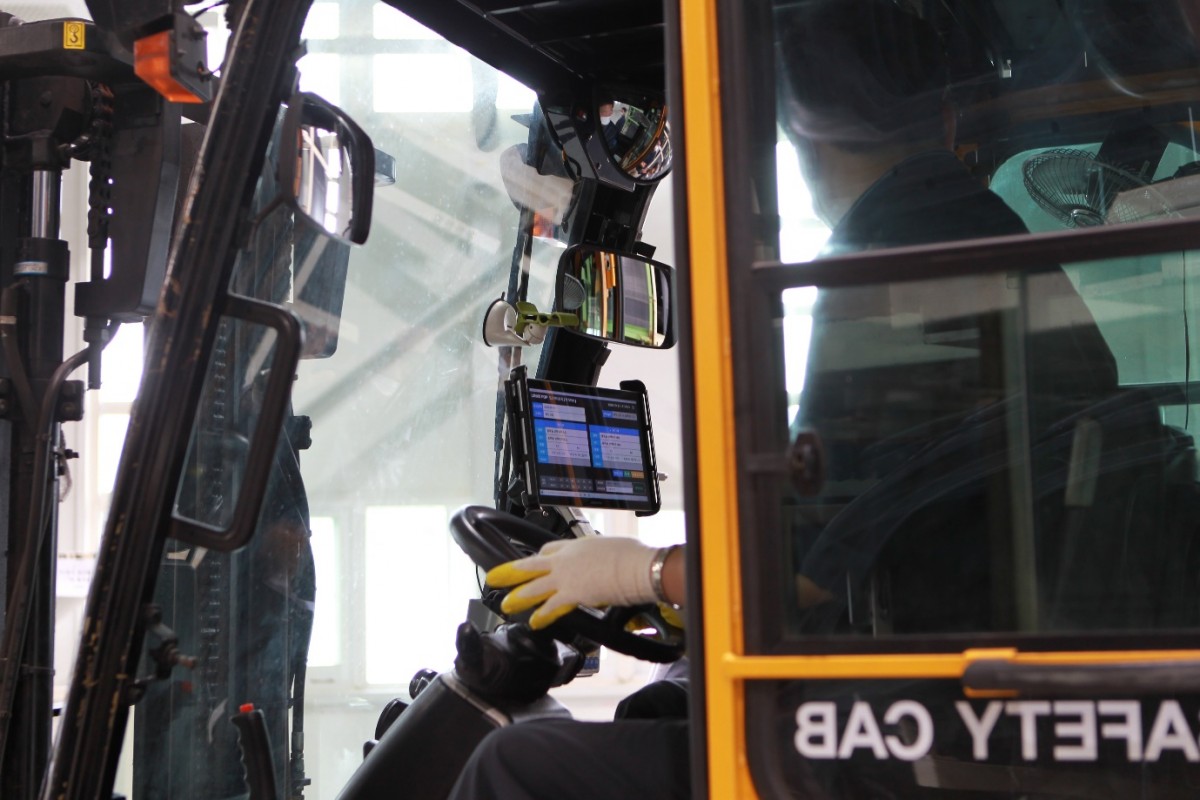
CPS를 활용한 원격 운영과 제어
텔스타는 지난 연말 ITS 2019(Coex), 한-아세안 EXPO(Bexco) 두 번의 전시회 참가를 통해 전시장에서 경주 현장 설비를 실시간 원격 제어하 는 시연을 선보였다. 원거리에서 설비를 정지시키고 재가동하는 간단 한 내용이었지만, 전시회에서 실제 가동 중인 공장을 실시간 제어한 사 례로는 최초였다. 그만큼 이론과 달리 리스크가 크고, 실제 구현이 어 려운 고도화 기술을 텔스타가 실현해낸 것이다. 여기에는 여러 가지 데 이터 관리 기술이 쓰였지만 그중에서도 CPS와 5세대 통신(5G)의 활용 이 큰 부분을 차지했다. 단순한 ‘원격 제어’ 의미를 넘어 CPS를 통한 공 장의 ‘원격 운영’을 목표로 하여 현재까지 설비 제어뿐만 아니라 GPS 를 통한 물류의 실시간 동선 분석, 공장 에너지 관리를 위한 유틸리티 제어 등이 추가되었다. 현재는 AR 기능을 추가하여 원격 생산 및 설비 상태의 확인, 원격 가동과 정지 지시도 구현되게 되었으며, AI 비전을 활용한 예지보전 시스템 적용 기술을 개발 중이다. 이처럼 실제 공장 을 Digital Twin으로 가상화하여 공장의 Data를 하나씩 연결해 나아간 다면, 결국 해당 공장이 전 세계 어디에 있더라도 텔스타는 실시간으로 공장 정보를 확인할 수 있다. 현재 본사(평택)에서는 우리가 구축한 각 스마트 공장 사이트의 종합 관제센터 구축을 검토하며 전문 엔지니어 링 서비스 기업으로 한 걸음 더 나아가고자 준비 중이다.
Remote operation and control by utilizing CPS
Telstar participated in two exhibitions at the end of the year, ITS2019 (Coex) and ASEAN-Korea EXPO (Bexco) where the company demonstrated real time remote control on equipment at Gyeongju site. It was a content that simply stops and restarts the equipment from a long distance, though it was the first time that the actual factory was controlled in real time at the exhibition. As such, unlike theory, Telstar has realized advanced technology that has high risks and difficulties in realization. For the demonstration, various data management technologies were used, but among them, the use of CPS and 5th generation communication (5G) took up a large part. It went beyond simple meaning of “remote control” and aimed to “remote operation” of the plant through CPS. In addition to the currently available equipment control, real-time movement analysis of logistics through GPS and utility control for plant energy management, and others were added. Currently, Telstar has added an AR function to enable remote production as well as equipment status confirmation, and remote start and stop order. In addition, it is developing a technology for applying the predictive maintenance system utilizing AI vision. In this way, if the actual plant is virtualized as a digital twin and the data of the plant are connected one by one, in the end, no matter where the factory is located in the world, Telstar can monitor the information in real time. Now the HQs (in Pyeongtaek) is reviewing the building a comprehensive control center for each smart factory site that it has built. Through this, Telstar is preparing to take one step further as a professional engineering service company.
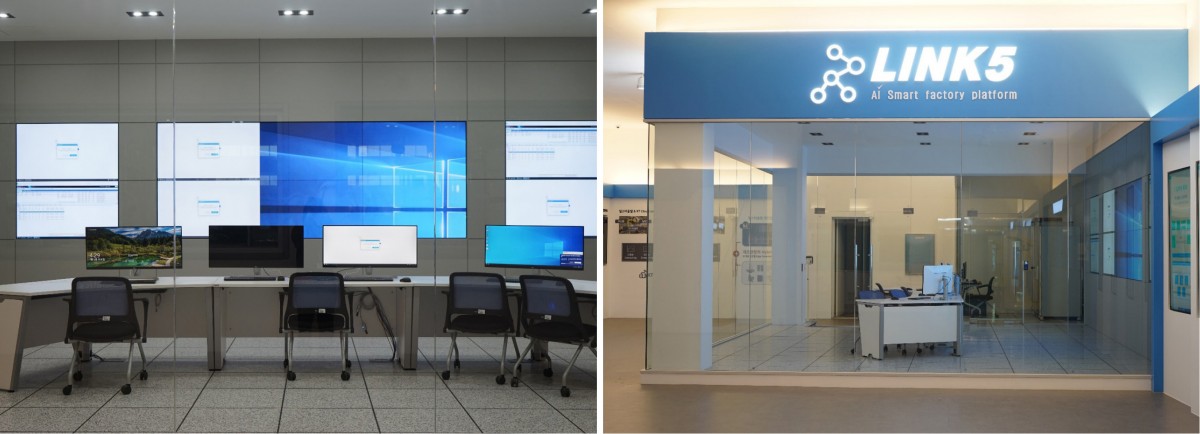
훈련된 데이터 분석을 통한 공장 최적화 운영 Optimized Control
공장 디지털화 → 실제 공장 가상화(Digital Twin) → 데이터 연결과 제 어가 가능하게 된 후에도 공장이 Q, C, D, R 관점에서 목표를 지속적으 로 달성하려면 끝없는 공장 운영의 조정이 필요하다. 텔스타의 비즈니 스 모델에서와 같이 스마트팩토리 사이클을 완성한 후에는 운영을 통 해 경험 데이터를 쌓을 수 있게 된다. 경험을 통해 얻은 결과 데이터는 목적에 맞게 다시 한 번 현장을 최적화하는 데 활용할 수 있다. 제조업 의 영원한 숙제인 Q, C, D, R 의 해결은 한 번에 이루어 낼 수 없는 어려 운 부분이다. 데이터 기반 운영을 통해 계속해서 최적화하며 유지하는 것이다. 텔스타는 경주 공장을 통해 우리의 비즈니스 모델을 현실 구현 하고, 시범 공장으로서 국내 모범 사례가 되길 소망하며, 전 세계 제2, 제3의 경주 공장을 수출하는 미래를 꿈꿔본다.
Optimized control and operation of a plant through an analysis on trained data
Endless adjustment on plant operation is required for a plant to continuously achieve a goal from the perspective of Q, C, D, R even after the process of plant digitalization → Actual virtualization of a plant → completion of data connection and control. As in Telstar's business model, after completing the smart factory cycle, experience data can be accumulated through operation. Data containing the results obtained through experience can be used to optimize the site once again for its purpose. Finding a solution for Q, C, D, R, an everlasting homework for manufacturing industry, is challenging and it cannot be achieved at once. That is why Telstar is continuously maintaining optimization through databased operations. Telstar has been striving for realization of the actual business model through the Telstar Gyeongju. I hope that Gyeongju plant become a best practice as a pilot plant domestically, and dream to export 2nd and 3rd Gyeongju plant globally
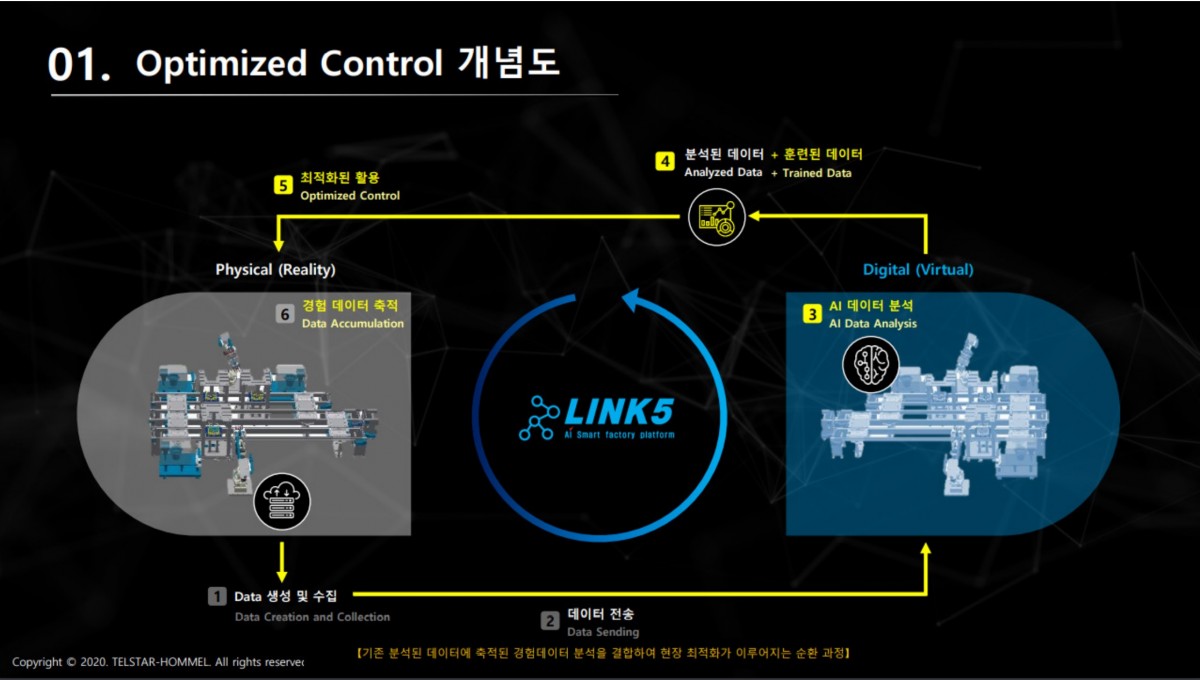